The Great Green Hope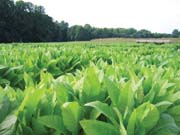
Protein and ethanol wrung from tobacco’s green leaves may bring the one-time cash crop back to Maryland fields
by Matt Makowski
Maryland tobacco crashed this week.
A mere 300,000 pounds went to market in the famous Maryland tobacco auction, where farmers follow the auctioneer down the bales to hear their fortunes told by buyers. More than a million pounds sold in both 2005 and 2004. Over two million sold the year before. In 2002, over three and a half million. In 2001, over eight million. That’s the story of Maryland tobacco.
But Maryland tobacco may rise from the dead.
Tobacco advisor Gary Hodge, bio-entrepreneur Neil Belson, scientist Robert Kratochvil and congressman Steny Hoyer don’t believe tobacco has gone up in smoke. Proteins could redeem the stigmatized crop. Its broad leaves could fuel industry.
“It really is exciting when you think of the many benefits in the context of rural development, replacing petroleum and reducing greenhouse emissions,” Belson said.
From Field…
For centuries, this has been the time of year tobacco farmers started new plants in warm greenhouses. By May, as the ground warmed, they’d transplanted their babies to warm seedbeds.
Twenty-first century tobacco farmer Robert Kratochvil, a PhD agronomist at the University of Maryland’s Agriculture Experiment Station, speeds up the labor-intensive process. At the end of next month, he’ll spray down his tobacco fields in Upper Marlboro with a seed-loaded hose. By direct-seeding, he can grow as many as 80,000 plants per-acre. That’s 12 times as dense as the 6,000 to 6,500 plants per acre farmers grew in olden times.
For protein and biomass, today’s tobacco farmers need volume rather than the delicate leaf that made Type 32 Maryland tobacco prized in the world cigarette market.
“Like they plant grass with a hydro-seeder, we’re attempting the same thing with tobacco seed,” Kratochvil said.
That’s not the only revolution in today’s tobacco field.
Farmers used to work 200 hours per acre of tobacco. Growing 12 times more tobacco would have meant a dreadful increase in backbreaking labor. To save their backs, Kratochvil and his team have mechanized their tobacco harvest, using traditional forage harvesters instead of hand-harvesting the field plant by plant.
The plants are harvested earlier, too, during their reproductive stage, when the flower starts to bloom. The forage harvester cuts the dense crop three to four inches above the ground so the stubs re-sprout a second crop. Kratochvil harvested not two but three crops last year.
… To Lab
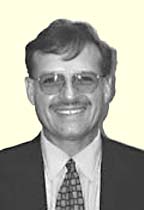 |
Twenty-first century tobacco farmer Robert Kratochvil tends his fields at the University of Maryland’s Agriculture Experiment Station, where his efforts yield industrial chemicals and energy-producing bio-mass.
|
The harvested crop bypasses Maryland’s tobacco-curing barns, another arduous stop in the traditional cycle of growing smoking tobacco. Kratochvil’s experimental crop heads straight to a processing plant on the campus of the University of Maryland.
Here food scientist Y. Martin Lo extracts the protein.
He works in a nondescript garage-looking building. The cement-floored space appears mostly empty, except for two important pieces of equipment on loan from North Carolina State University.
“This is a hammer mill,” Lo said, showing off what looks to the non-scientist like your average conveyor belt. From the belt, tobacco is carried up toward a metal cutting box where knives hack it into tiny shreds about the size of spices in your pantry. The finely hewed tobacco is then hand-carried to the other centerpiece of the room.
“This squeezes out the juice that holds the proteins,” Lo said of his screw press. This tool is simple enough. A large chute is loaded with tobacco, and a motor spins a large screw that crushes the tobacco against a wall. Out of the bottom comes the protein-laden juice. Except for its size and motor, it’s not unlike a home meat-grinder.
The olive-colored juice that comes out of the screw press is far from consumer ready. Lo takes the payload to his lab, which is not-so-conveniently on the other side of campus. He pours the juice into a centrifuge that spins the fluid and separates the solids, breaking them into parts. Some parts are useful, some aren’t. The green chlorophyll isn’t needed. The amino acids and proteins are. When the proteins are pulled, the nicotine and tar — which ended tobacco’s old reign — are left behind.
Payload
The protein payload will, with any luck, be the golden egg that keeps the tobacco goose thriving. Four departments at the University of Maryland are collaborating to make it so. Together with Gary Hodge and Neil Belson, they are researching how to use tobacco proteins as a beneficial additive to personal care products. In hand lotions, tobacco could accelerate healing and reduce signs of aging. In shampoos, the proteins could help strengthen hair and give it that fresh-from-the-beauty-parlor shine. There is also potential for the protein in vitamins and pet food.
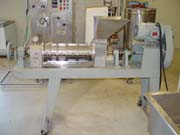 |
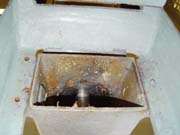 |
Uncured tobacco plants are first fed into the hammer mill, above, which carries the plants to a metal cutting box where knives hack it into tiny pieces. From there, the tobacco is carried to a screw press, above and right, which squeezes the vegetation to a pulp, extracting an olive-colored juice that, when refined, is a beneficial additive to personal care products like shampoo, hand lotion and even vitamins.
|
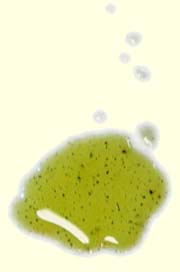 |
The tobacco pulp is a second payload in the form of biomass. Using a process similar to fermentation, the team hopes to transform the leftovers into ethanol. Turned into the hot-burning fuel, the diced remains can replace the petroleum in industrial chemicals like dyes, cleaning agents or even plastics. The renewable biomass can yield energy while emitting far fewer greenhouse gases than does fossil fuel.
Tobacco’s Ticking Clock
The clock is ticking. Since 1998, 83 percent of Maryland tobacco farmers have signed 10-year-long Tobacco Buyout Agreements. In that buyout, Maryland used part of its National Tobacco Settlement Agreement money to persuade tobacco farmers to give up their crop. The state’s intent was to reduce smoking, not farming. To support continued farming, tobacco farmers who signed up had to retain their land for 10 years in some form of agriculture — anything but tobacco. In return, the farmers receive a check equal to the amount of money they would have earned from tobacco. When those 10 years are up, the farmer has a new decision to make: stick with the farm or sell it for ready money?
“The most ideal situation for them would be to continue farming tobacco,” Hodge said. “That’s what they’ve been doing for generations. And that certainly would be the easiest transition for them to make.”
It’s the same tobacco that the farmers have been growing for generations. Only the methods and the uses would be different.
Over the next two years, the team will be working on refining the technology for pulling out the proteins. The next step is to build a larger processing plant
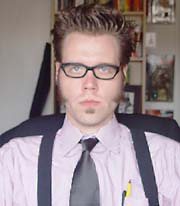 |
Matt Makowski, of Annapolis, is a journalism graduate of Rutgers University. This is his first story for Bay Weekly.
|
to extract the proteins in quantities large enough to find customers for the product. That’s where new-age tobacco f
armers step in.
Then it’s onto a full-scale commercial facility, the moneymaker in tobacco’s new equation.
“The tobacco farmers have been getting hit in the purse because of the declining desire for cigarettes,” said U.S. Rep. Steny Hoyer, who guided more than one million dollars in federal funding to the alternative use project. “They’re
going to be the biggest beneficiaries.”
Even as the market for tobacco shrinks, another stigmatized crop has grown in popularity thanks to technology and creative marketing. Cannabis, or hemp as it is called when grown for reasons other than smoking, has boomed over the past 15 years. Germany now uses the fiber in car panels. In the United States, hemp seeds are ingredients in a range of food products and cosmetics. If marijuana gets a new name when it’s being grown for non-smoking purpose, perhaps tobacco should be graced with the same consumer-friendly advantage. Maybe people would be more willing to wash their hair with “broadleaf” proteins than tobacco proteins — even if it is the same thing.